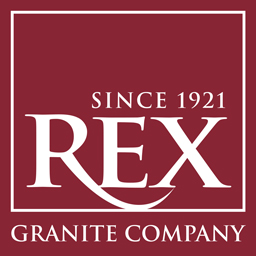
In the earliest days of monument building, processes were labor intensive and time consuming. We’ve come a long way since then, parti
In the earliest days of monument building, processes were labor intensive and time consuming. We’ve come a long way since then, particularly when it comes to sandblasting. Here we'll run down some of the key advancements in the world of granite sandblasting that have moved our industry forward over the decades.
Before air tools were available, lettering was all chiseled on using hand tools. Eventually, the process was improved through the use of air tools. Air tools excelled particularly at creating V-Sunk or Round Raised style lettering.
In the 1940's and 50's, the bar was raised with the introduction of glue. The glue was heated in a pot, poured on the stone, leveled off, and allowed to dry. Upon drying, it was cut through with a knife allowing the sand and high-pressure air to engrave the letters onto the stone. All of the artwork was done by hand on paper and subsequently transferred onto the glue.
Next, the 3M Anchor stencil that we still use today became commonplace in the 1960's and 70's, coming in rolls of different widths. This sped up the process substantially, but with hand cutting still involved on all of the stencil, it still wasn't as fast as today's computer powered machines.
In the 1980's, computer software revolutionized the process of lettering granite. With new programs and cutting plotters available, the world of digital artwork and monument sandblasting intersected. The ability to digitize and scan custom work brought the granite industry ahead leaps and bounds. The use of cutting plotters allowed manufacturers to achieve near-perfect precision, with the stencil being applied directly to the memorial. This step saved major time and labor, especially with the introduction of pre-cut stencil - another lynchpin for a fast and easy production process.
Similar to the evolution of lettering, sandblasting technology was nonexistent in the earliest days of granite and hand chisels were only tool for the job at hand. Eventually, air compressors were introduced and blasting started being done in dedicated rooms. Originally, the job required intense labor with a single person having to hold the hose and nozzle of the sandblaster and move it to precise locations to achieve quality lettering.
Eventually, automatic sandblasting was introduced by a few memorial dealers in the Midwest. The machine was able to move hose and nozzle to precise locations using hydraulics and manual stopping points, allowing this efficient process to be left unattended in most cases.
Finally, the Sandhandler was invented by a southern memorial dealer. This machine introduced CNC technology into the memorial sandblasting world and made the process incredibly efficient and precise. The combination of speed and accuracy, along with complete unattended auomation has crowned the Sandhandler as the gold standard in sandblasting technology to this day.
While other aspects of sandblasting and lettering have seen major technological improvements, the process behind adding floral elements or roses to a monument has not changed dramatically. This kind of work still requires a level of detail and touch that only a human can provide. The only difference being the setting in which shape carving takes place. For years, we had the operator gdo so inside the blasting room. Nowadays, we can handle the process outside the blasting room.
We specialize in the production of high-quality granite memorials and monuments. We offer a wide range of both domestic and international colors and can accommodate any design requirement for our B2B partners, including funeral homes and cemeteries.